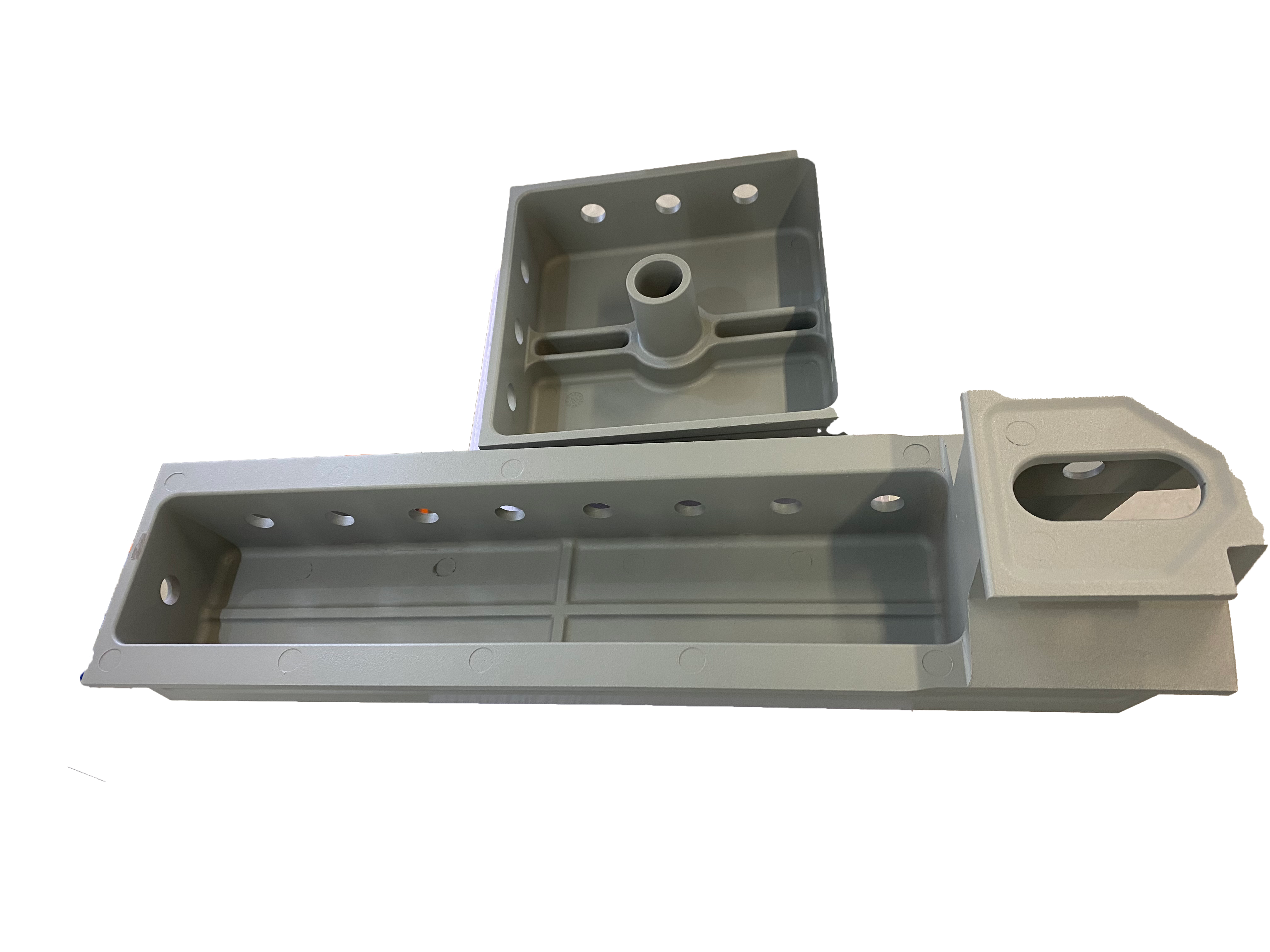
Defect features:
During the die-casting and pouring process, the slag or impurities in the alloy liquid are wrapped by the flow of the alloy liquid and participate in the mold cavity together with the die-casting and filling process. After cooling and solidification, holes (sometimes slag, sometimes chips) are formed in the casting, leaving holes or foreign objects on the machined surface after machining. Because it is caused by slag, oxide scale, it is irregular, the surface is not only irregular, but the whole or part of the pores are filled with slag, etc.
How to find:
Visual inspection after machining or x-ray inspection.
Cause analysis:
- During the alloy smelting process, slag or foreign matter is mixed into the alloy liquid.
- There are too many impurities and sundries in the alloy material.
- In the process of alloy smelting, refining degassing and slag removal (slagging, slag removal) are incomplete and cannot play an effective role. Or the refining agent itself is not pure.
- During the alloy refining process, the refining temperature is too high and the alloy viscosity is too high, so that the slag is not easy to float from the liquid surface, so the removal effect cannot be achieved. Alternatively, the alloy liquid has low temperature and low flow. Too low casting temperature will result in the free state of silicon in the Al-Si alloy.
- During the alloy refining process, the stirring is too strong, and the slag is related to the alloy liquid.
- When the alloy is refined, the standing time is short, and the slag cannot float.
- The overflow tank on the mold is not set correctly, and the overflow tank cannot collect the slag.
- Splash during filling, which forms oxide inclusions in the alloy during filling.
- There is dirt in the material tube, the soup pressure head is dirty, and the mold cavity is dirty. During the filling process, too much black lead oil entered the mold cavity.
- Recycling charges contain large amounts of water or oil.
Precaution:
- Material selection should be made from relatively pure alloy ingots. All charges put into the furnace must not be mixed with greasy dirt, water, debris and other substances that may produce slag and substances.
- Carry out refining and slag removal in strict accordance with the operation requirements. The deslagging must be dried first and the purity is high.
- Appropriately increase the charging temperature to facilitate the muck.
- Completely eliminate all foreign matter that may come into contact with the alloy liquid.
- On the premise of ensuring the normal operation of the soup, try to use less black lead oil.
- Clean the smelting furnace (parts) and its smelting tools in time.
- During the long-term heat preservation process, do not intentionally or unintentionally damage the alloy liquid on the surface of the alumina protective film to prevent the strengthening oxidation of the alloy.
- Magnesium-containing aluminum alloys are prone to oxide slag.
- Aluminum alloys with high copper and iron content are prone to generate free silicon.
Conclusion
For more information about oem aluminum die casting parts,aluminium die casting parts factory,aluminium high pressure die casting parts, we are glad to answer for you.