Thread milling method
- Characteristics of thread milling
Thread milling adopts a thread milling tool and a three-axis linkage of machining center, that is, x-axis and y-axis arc interpolation, and z-axis linear feed milling method to process threads.
Thread milling is mainly used for machining large hole threads and threaded holes of difficult-to-machine materials. It mainly has the following characteristics:
- fast processing speed, high efficiency, and high processing precision. The cutting tool material is generally cemented carbide material, and the cutting speed is fast. The manufacturing accuracy of the cutter is high, so the milling thread accuracy is high.
- milling tools have a wide range of applications. As long as the pitch is the same, whether it is a left-hand thread or right-hand thread, a tool can be used, which is conducive to reducing the cost of tools.
- milling is easy to remove chips and cool, and the cutting condition is better than that of the tap. It is especially suitable for thread processing of difficult-to-machine materials such as aluminum, copper, and stainless steel. It is especially suitable for thread processing of large parts and components of valuable materials, which can ensure the quality of thread processing and the safety of the workpiece.
- because there is no tool front-end guide, it is suitable for processing blind holes with short thread bottom holes and holes without tool withdrawal grooves.
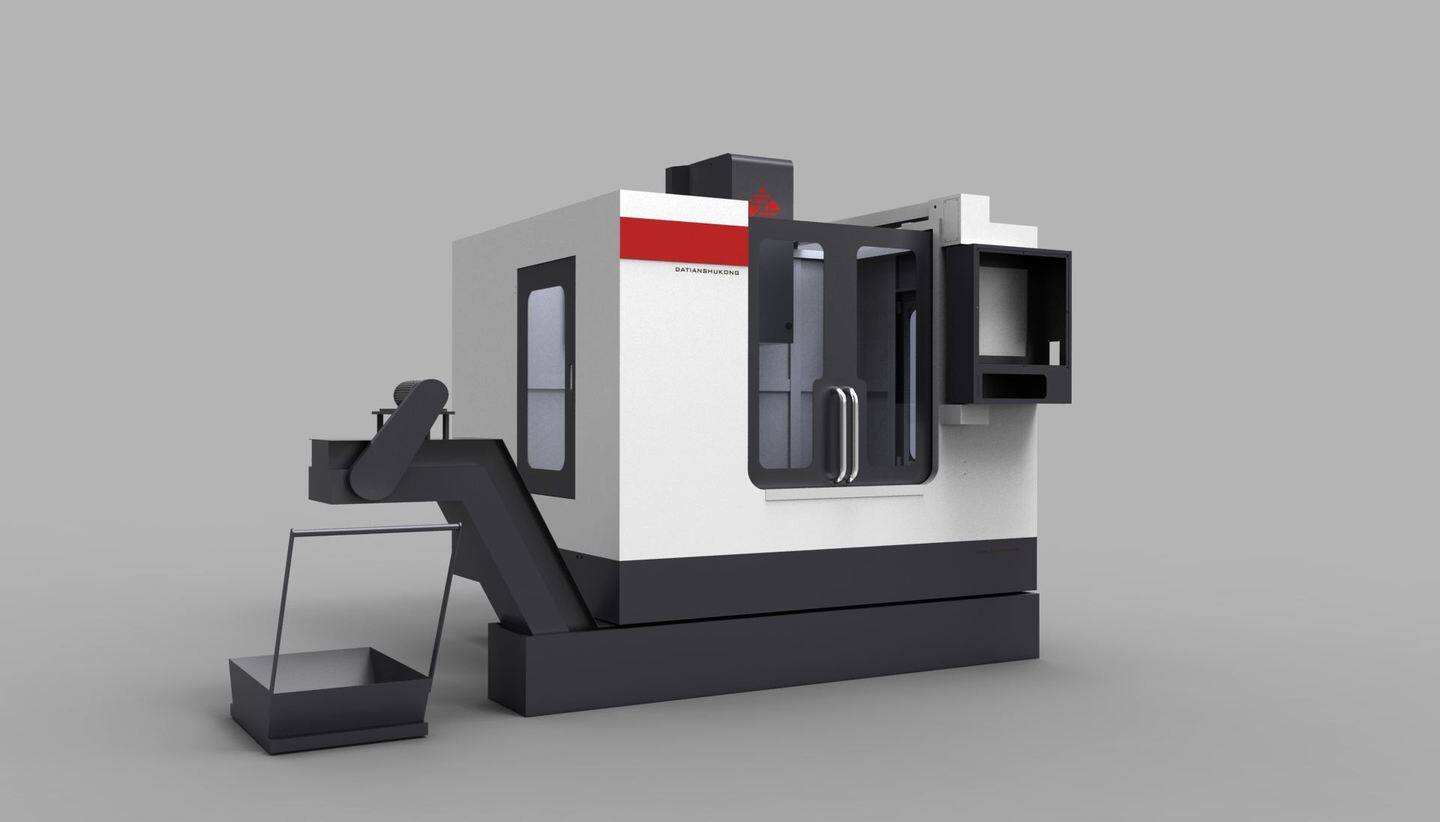
- Classification of thread milling tools
Thread milling tools can be divided into two types, one is a machine clamp carbide blade milling cutter, and the other is an integral carbide milling cutter. The clamping tool has a wide range of applications. It can process holes with tread depth less than the length of the blade or holes with thread depth greater than the length of the blade. An integral carbide milling cutter is generally used to process holes with tread depth less than the length of the cutter.
- CNC programming of thread milling
The programming of thread milling tools is different from that of other tools. If the processing program is wrong, it is easy to cause tool damage or thread processing errors. Attention should be paid to the following points during preparation:
- first, the bottom hole of the thread should be processed well, the small-diameter hole should be processed with a drill, and the larger hole should be bored to ensure the accuracy of the bottom hole of the thread.
- when cutting in and cutting out, the cutter should adopt the arc track, usually 1/2 circle, and at the same time, the z-axis direction should travel 1/2 pitch to ensure the thread shape. The tool radius compensation value should be brought in at this time.
- when the X and Y axes are interpolated for one circle, the main shaft should travel a pitch along the Z-axis direction, otherwise, the threads will be screwed disorderly.
- specific example program: the diameter of the thread milling cutter is Φ 16. The threaded hole is M48 × 1.5, and the depth of the threaded hole is 14.
Snap method
- Characteristics of snap method
Large threaded holes can sometimes be encountered on box parts. In the absence of taps and thread milling cutters, a method similar to lathe thread picking can be used.
Install the thread turning tool on the boring bar to bore the thread.
The company once processed a batch of parts, the thread is m52x1.5, and the positional degree is 0.1mm (see Figure 1). Because the positional degree requirements are high, the threaded hole is large, it is impossible to use a tap for processing, and there is no thread milling cutter. After testing, the thread picking method is used to ensure the processing requirements.
- Precautions for buckle method
- after the spindle is started, there should be a delay time to ensure that the spindle reaches the rated speed.
- when withdrawing the tool, if it is a hand-ground thread tool, because the tool cannot be ground symmetrically, it cannot be reversed. The spindle orientation must be adopted, and the tool moves radially, and then the tool is withdrawn.
- the manufacturing of the cutter bar must be accurate, especially the position of the cutter groove must be consistent. In case of inconsistency, multi-toolbar machining cannot be adopted. Otherwise, it will cause disorderly deduction.
- even if it is a very thin buckle, you cannot pick it with one knife, otherwise, it will cause tooth loss and poor surface roughness. At least two knives should be divided.
- the processing efficiency is low, which is only applicable to a single small-batch, special pitch threads, and the absence of corresponding tools.
Summary
To sum up, the methods of processing threads in the CNC machining center mainly include tap processing, milling processing, and thread pick method. Tap processing and milling processing are the main processing methods, and the thread pick method is only a temporary emergency method. Only by correctly selecting thread processing methods and processing tools, can we effectively improve the efficiency and quality of thread processing, improve the efficiency of the CNC machining center, and reduce processing costs. Every NC processing technician should be proficient.
Searching for a used machining centers for sale, vertical and horizontal machining center, 5 axis machining center for sale supplier, wholesaler, manufacturer from China, you can get high-quality products at a nice price.